Checking Out the Different Methods of Light Weight Aluminum Spreading: A Comprehensive Guide
Light weight aluminum casting stands as an essential process in the production of various items we come across daily, from elaborate auto elements to household fixtures. Recognizing the diverse approaches utilized in light weight aluminum casting is critical for makers looking for precision and performance in their production procedures - aluminum casting. As we embark on this expedition of the various methods associated with aluminum spreading, we uncover a world where innovation and custom merge to shape the products that form our modern globe
Sand Spreading Method
Using among the oldest and most commonly made use of methods in aluminum spreading, the sand spreading method involves producing molds from a mix of sand and a binder product. This strategy is highly versatile, economical, and ideal for producing a vast array of sizes and shapes, making it a prominent option in numerous sectors.
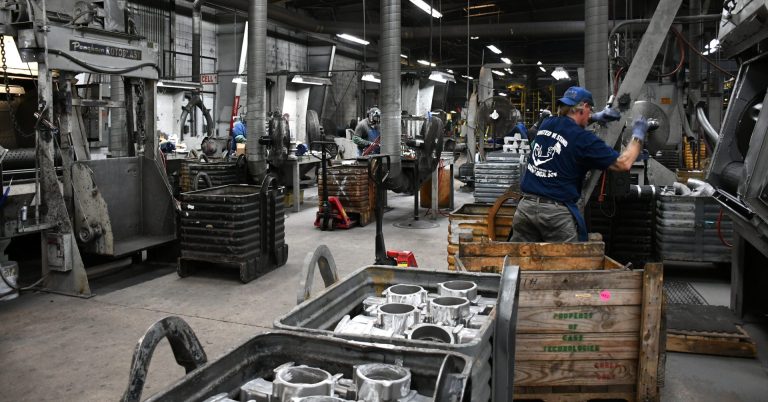
Aluminum, warmed to its melting point, is after that poured right into the mold, loading the cavity. After cooling down and solidifying, the sand mold and mildew is escaped, disclosing the aluminum spreading. This method permits the production of complicated geometries and is well-suited for both low and high volume manufacturing runs.
Investment Casting Method
Having actually explored the sand spreading method, a refined strategy to aluminum spreading is the financial investment casting method, which offers unique benefits in terms of precision and surface area coating. Investment casting, additionally called lost-wax casting, is a procedure that involves producing a wax pattern that is covered with a ceramic shell. Once the covering is dried out and hardened, it is heated to get rid of the wax, leaving a hollow ceramic mold. Molten aluminum is after that put right into the cavity, filling up the mold and mildew to develop the desired part.
One of the primary benefits of financial investment spreading is its ability to generate complex shapes with high precision and intricate details. The process allows for thin walls, sharp sides, and great surface area coatings that call for very little post-processing. Furthermore, financial investment spreading is understood for its exceptional dimensional accuracy and tight tolerances, making it a preferred approach for generating components that need tight specifications. In general, the investment spreading strategy is a functional and efficient method for making high-grade light weight aluminum elements.
Permanent Mold And Mildew Process

One of the key advantages of the Long-term Mold Process is its capacity to generate parts with a finer grain structure, resulting in boosted mechanical properties. In addition, the recyclable nature of the metal mold and mildew permits for the production of a a great deal of components with constant high quality. This method is commonly made use of in the automobile, aerospace, and aquatic markets for producing components such as engine pistons, wheels, and architectural parts. By leveraging the Irreversible Mold Refine, makers can achieve cost-effective manufacturing of aluminum get rid of exceptional dimensional accuracy and surface coating.
Die Casting Technique
In comparison to the Permanent Mold Process, the Pass Away Casting Strategy for light weight aluminum casting involves using a multiple-use steel mold and mildew to produce elaborate get rid of high dimensional precision. This technique is extensively made use of in various markets due to its ability to effectively manufacture complicated forms with slim wall surfaces and superb surface area coatings.
Pass away casting typically begins with the preparation of the steel mold, which is then sprayed with a lubricant to help with the removal of the solidified aluminum. The mold is closed, and molten aluminum is infused under high stress right into the dental caries. When the light weight aluminum solidifies and cools, the mold and mildew opens up, disclosing Source the completed part.
One of the essential advantages of die spreading is its high manufacturing price, making it an affordable service for large-scale manufacturing. In addition, components generated with die casting exhibit superior toughness and toughness contrasted to those made with other casting approaches. This technique is especially suitable for applications requiring intricate layouts, tight tolerances, and high repeatability.
Centrifugal Spreading Technique
How can the Centrifugal Spreading Technique enhance the performance and high quality of aluminum spreading processes? Centrifugal casting is an approach that uses centrifugal force to disperse molten steel into a mold and mildew tooth her comment is here cavity. This technique supplies a number of advantages over typical casting approaches.
One secret benefit is the remarkable quality of the spreadings produced. The centrifugal pressure helps to remove porosity by pushing any kind of gas or pollutants in the direction of the center of the spreading, resulting in a denser and extra uniform last product (aluminum casting). In addition, the rotational motion of the mold and mildew ensures a much more also distribution of the liquified metal, causing boosted mechanical properties and minimized defects
In Addition, the Centrifugal Casting Approach is known for its effectiveness. The quick solidification rate accomplished via this process can add to reduced cycle times, making it an affordable option for high-volume manufacturing. The method enables for the spreading of detailed shapes and thin-walled components with convenience, expanding the design opportunities for suppliers. To conclude, the Centrifugal Spreading Method attracts attention as a trustworthy strategy for boosting both the performance and quality of aluminum spreading processes.

Final Thought
To conclude, the different approaches of aluminum spreading provide special advantages and attributes for various applications. Sand casting supplies flexibility and cost-effectiveness, financial investment spreading enables for detailed styles, irreversible mold process makes certain premium coatings, die casting supplies high manufacturing rates, and centrifugal casting creates high-strength parts. Understanding the differences in between these approaches can help producers select one of the most suitable technique for their particular spreading demands.
Having explored the sand casting method, a refined technique to light weight aluminum spreading is the financial investment spreading technique, which offers distinct advantages in terms of precision and surface finish. Financial investment spreading, likewise understood as lost-wax spreading, is a procedure that entails developing a wax pattern that is covered with a ceramic covering.Exactly how can the Centrifugal Spreading Technique improve the effectiveness and top quality of light directory weight aluminum spreading procedures? In final thought, the Centrifugal Spreading Technique stands out as a trusted technique for enhancing both the efficiency and quality of light weight aluminum spreading procedures.
Sand spreading uses adaptability and cost-effectiveness, financial investment casting allows for elaborate styles, permanent mold procedure makes certain high-grade coatings, pass away casting supplies high production rates, and centrifugal spreading generates high-strength elements.